The future of
manufacturing is
rapid plasma deposition®
Norsk Titanium Expands Rapid Plasma Deposition® Application with Two New Customers
Norsk Titanium rapid plasma deposition® (RPD®) is a commercial aerospace OEM-qualified additive manufacturing process that delivers structural titanium parts with reduced lead time and cost. The future is now.
-
Technology
RPD® is fast, efficient, OEM-qualified, and now in production.
-
Advantages
RPD®‘s competitive advantage is delivering greater capacity at faster rates with much less material waste.
-
Company
RPD® is pioneering the next industrial revolution; be a part of the future of additive manufacturing.
How We’re Different
Norsk Titanium is the only high deposition rate additive manufacturing company that is:
-
FAA-approved and OEM-qualified for structural titanium parts manufacturing
-
Established to handle high-volume parts manufacturing on site or at your facility
-
Using process control and global configuration to enable machine-to-machine consistency
Rapid Plasma Deposition®
Titanium wire, argon gas, plasma arc, and process controls are at the heart of RPD®, resulting in Forged Strength at the Speed of Innovation®. Norsk Titanium provides treatment of materials, namely metals and metal ores by plasma arc additive layer manufacturing.
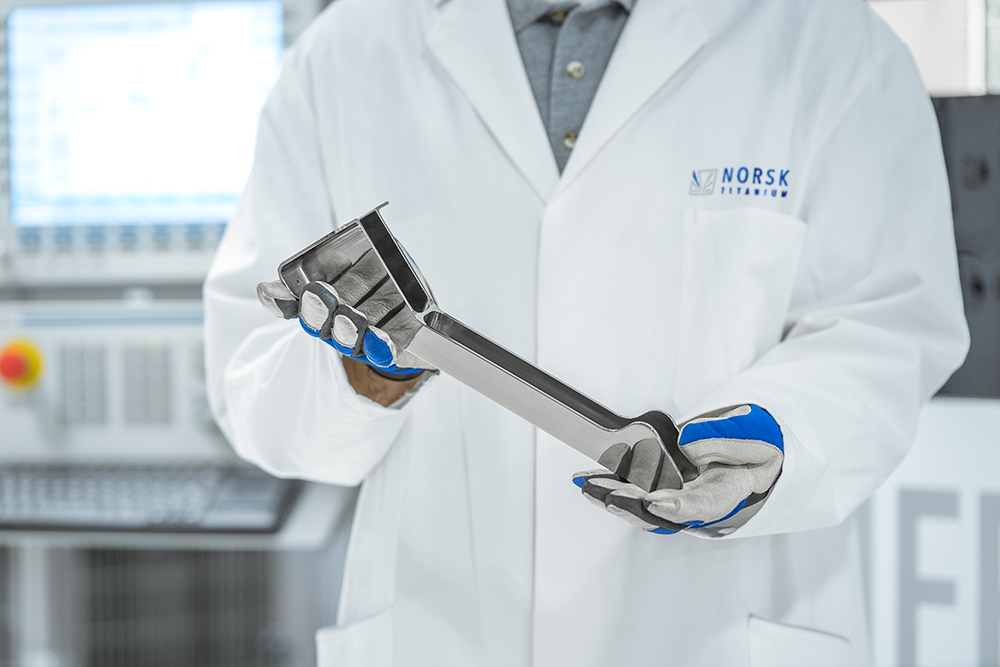
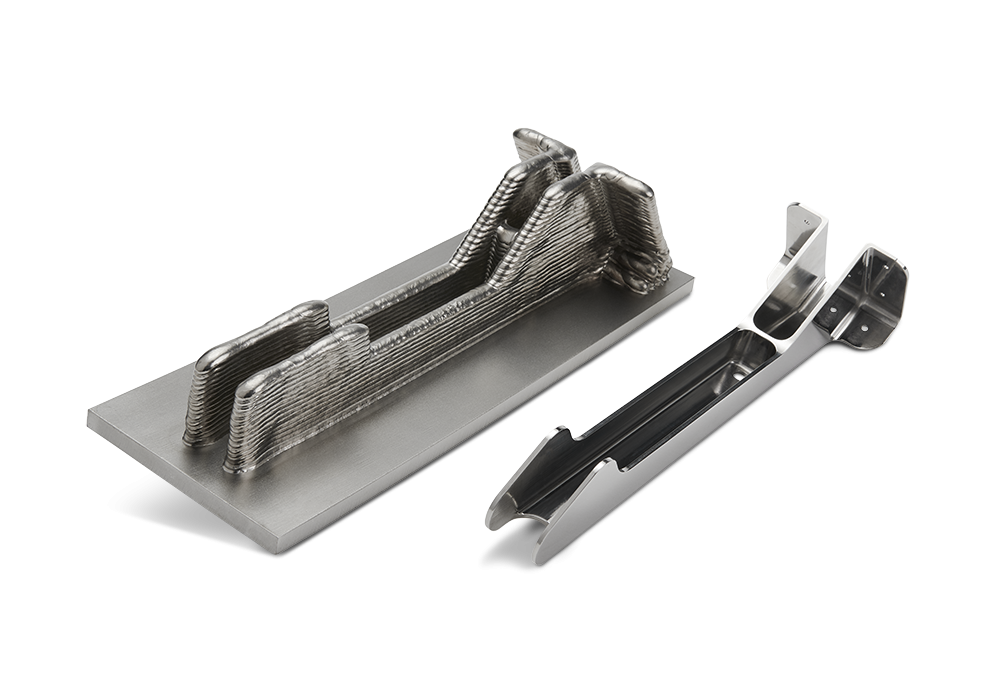
Norsk Titanium’s proven production capabilities deliver lower cost, less machining, less material used, and reduced lead time. Our MERKE IV® machine is the world’s fastest titanium printer in commercial production today. The MERKE IV® is 50–100 times faster than powder-based systems, while using 25%–50% less titanium than traditional forging.